igus® bearings ensure a maintenance-free bottling system
Self-lubricating polymer bearings from igus enhance efficiency at Belgium’s Chimay Trappist Brewery
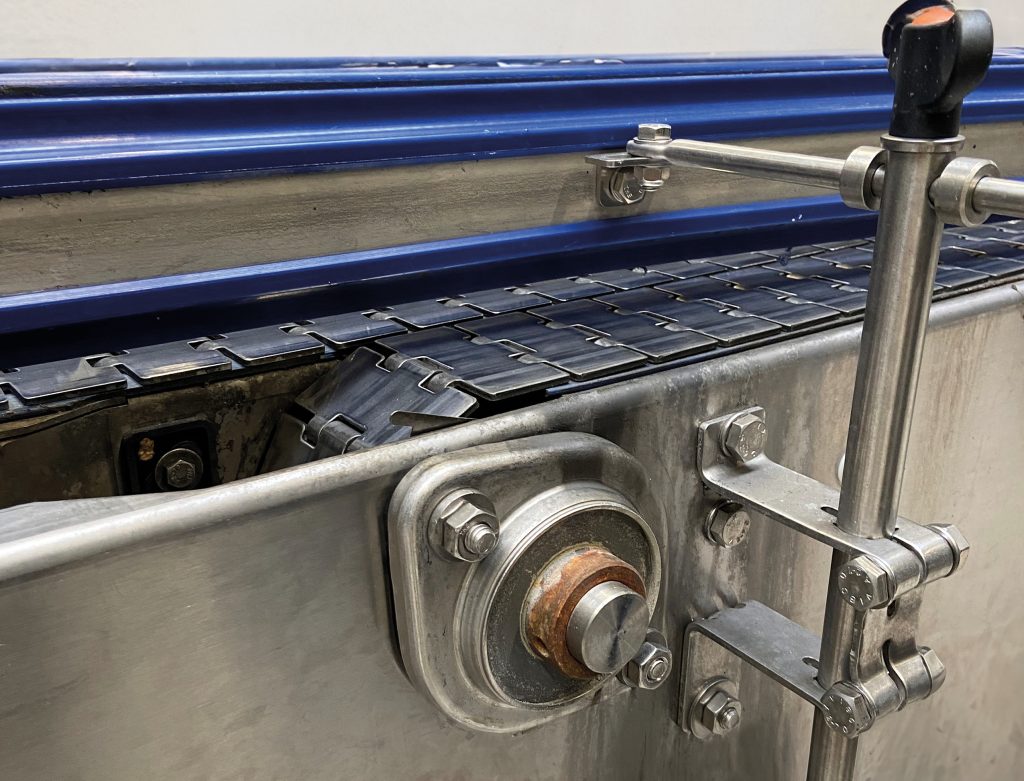
24 OCTOBER 2024 – Chimay Brewery, one of the world’s twelve producers of authentic Trappist beer, has successfully improved the efficiency of its bottling system by integrating dry-running spherical bearings from igus. The brewery, known for its traditional brewing methods at the Notre-Dame de Scourmont Abbey in Belgium, replaced conventional metallic ball bearings with igus igubal® H3 bearing inserts, reducing maintenance requirements and enhancing overall performance.
Chimay Brewery, which has been producing Trappist beer since 1862, encountered significant operational challenges with its bottling lines. Frequent failures and seizing of metallic ball bearings in the conveyor systems had become common, leading to costly downtime. In some cases, replacing a defective bearing could take up to one and a half days, disrupting production and causing financial losses.
A Maintenance-Free Solution
As part of a strategic initiative to optimize its production lines, Chimay partnered with igus to address the recurring issue of bearing failure. After extensive tests, the igubal H3 bearing insert from igus was selected as the ideal solution. Installed in September 2022, these high-performance plastic bearings have demonstrated minimal wear, with no instances of shaft damage or production delays since their implementation.
The igubal H3 bearing is made from tribologically optimized polymers, ensuring it remains lubrication-free, maintenance-free, and corrosion-resistant. These characteristics have proven particularly advantageous in the demanding environment of a brewery, where frequent cleaning cycles and chemical exposure can quickly degrade conventional bearings. The igubal H3’s ability to function without lubrication minimizes maintenance efforts and helps avoid contamination, a crucial consideration in food and beverage production.
Improved Performance and Durability
The switch to igus bearings has substantially impacted Chimay’s bottling process. Operating at speeds of up to 200 revolutions per minute (rpm) and achieving production rates of 55,000 bottles per hour, the new bearings have significantly increased productivity. Moreover, the easy-to-install igubal H3 bearing inserts have drastically reduced maintenance time, allowing for rapid replacement without specialized tools or extensive labor.
In addition to their efficiency benefits, the igubal H3 bearings are highly resistant to chemicals and cleaning agents, ensuring durability in a rigorous cleaning environment. This resistance, combined with their corrosion-free design, has extended the service life of the entire system, contributing to long-term cost savings for the brewery.
Scaling the Solution
Following the successful trial of the igubal H3 bearings on three production conveyors, Chimay has ordered 150 additional bearing inserts to replace the remaining metallic ball bearings throughout its bottling plant. The transition to these lubrication-free bearings has provided a sustainable, low-maintenance solution, allowing the brewery to continue focusing on producing its renowned Trappist beer.
“With the igubal H3 bearings, we have been able to solve the most important problem on our conveyor systems and significantly extend the service life of our equipment,” said Vivien De Schryver, Maintenance Technician at Chimay Brewery.
Learn more about igubal self-aligning bearings here: https://www.igus.com/spherical-bearings